NEWS
What is calibration? What does measurement calibration mean?
Everything is based on measurements
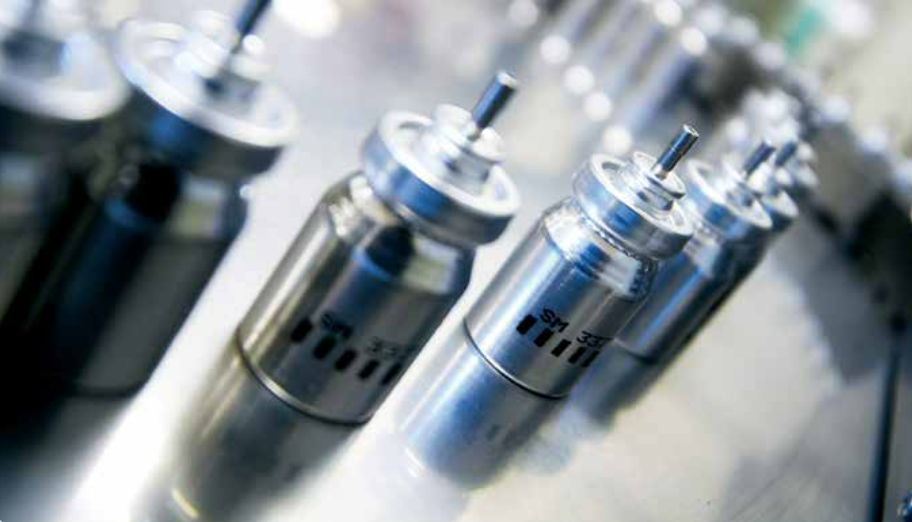
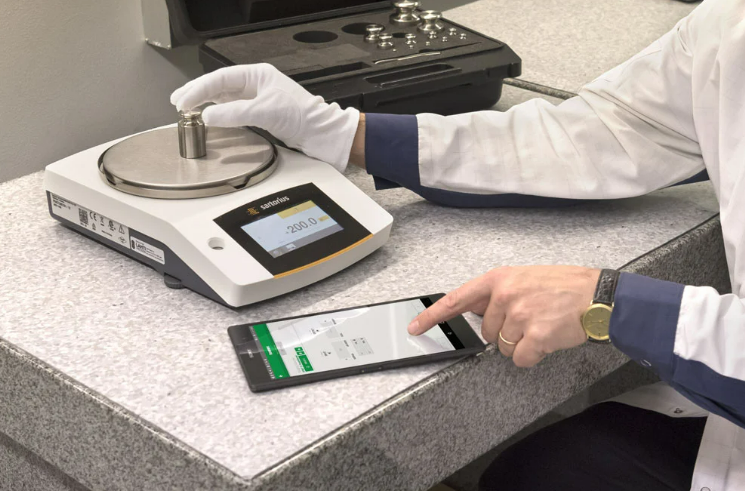
Calibration is key
What is an adjustment?
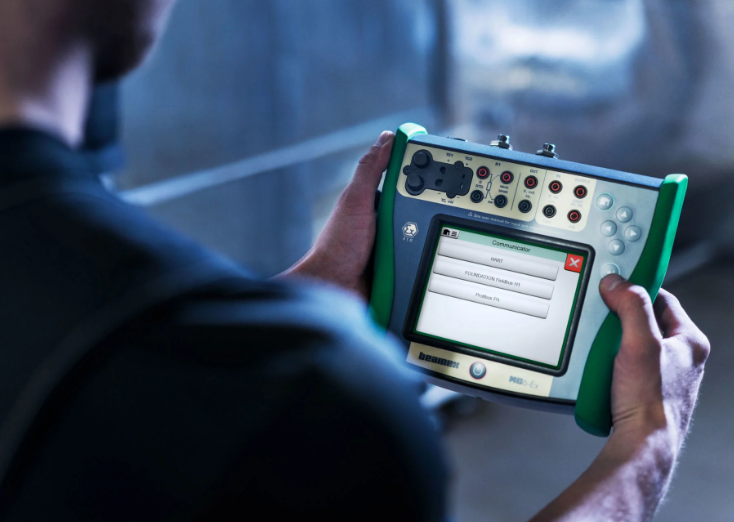
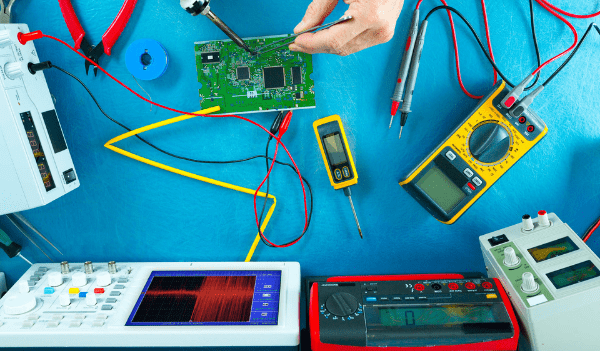
Digital calibration data stream
Conclude
Calibration of process equipment is the comparison and recording of equipment measurements with a traceable reference standard. It's important to calibrate so you can be confident that your measurements are valid. Measurement validity is important for many reasons, including safety and quality. For best results and reliability, make sure the calibration uncertainty is small enough. Use a calibrator that has accurate specifications many times better than the device being tested. Ultimately, setting tolerances and calibration frequency should be determined by a number of factors, including the criticality of the device.
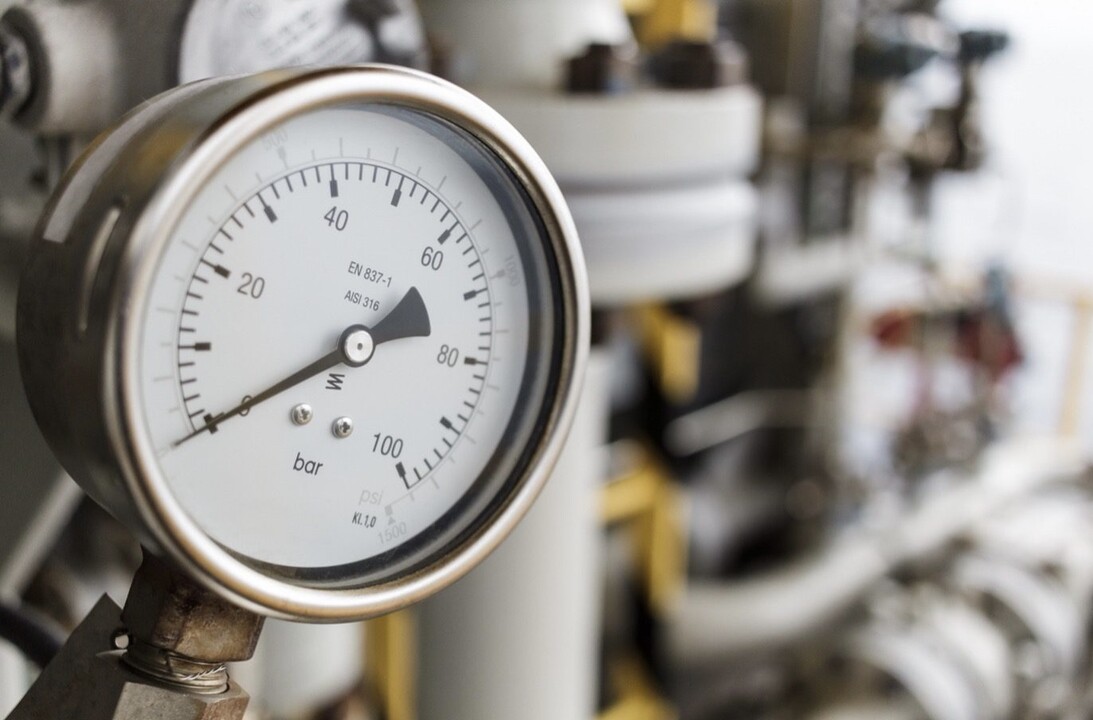
About me
Why should you calibrate?
+245
Finished projects
+12
Years of expierence
+11400
Hours filmed
+65
Motion graphics
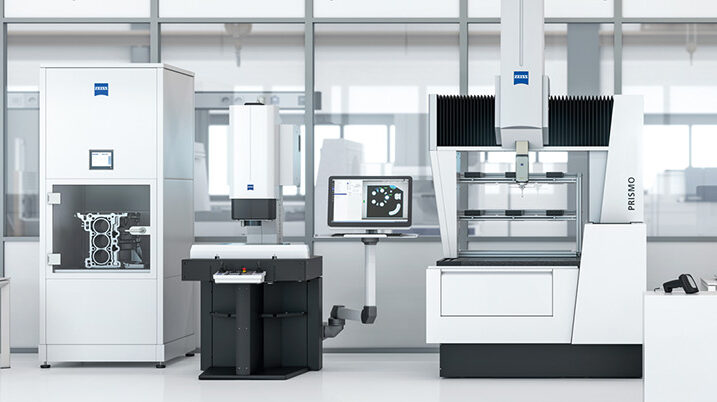
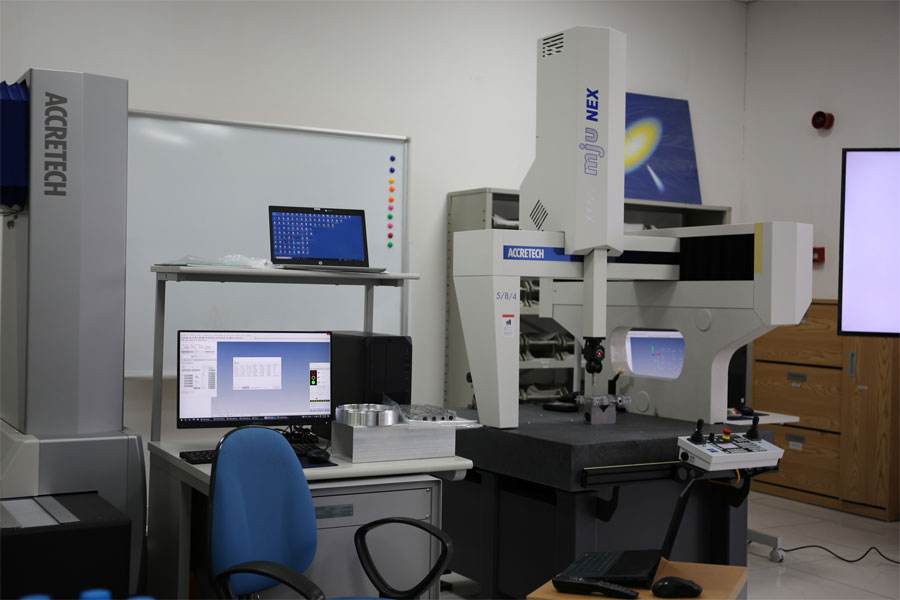
Learn about CMM Measuring Machine
CMM measuring machine also known as CMM machine (Coordinate Measuring Machine) is a type of machine used to measure and determine the shape of a complex surface by touching points on that surface or using light, rays, or beams to measure. Measure the dimensions of machine parts. CMM machines have the ability to measure and determine the exact position of points in a 3-dimensional space by touching that surface with a probe.
Right at the moment the probe touches the surface to be measured, the contact sensor on the CMM measuring probe will record information about the position of that touching point. Then, a point will be positioned in the 3-dimensional space that the CMM machine draws. And by touching many times at many different locations of the surface, the CMM Machine easily simulates that surface in 3-dimensional space.
At this time, the measurement results on that space will tell us the actual size and distance of the machine part that we need to measure. CMM machines can not only measure straight line dimensions, they can also measure diameter, radius, curvature, ovality or check the flatness of a surface...
CMM measuring machines are widely used in the manufacturing industry, especially in the mechanical processing industry. Nearly every machining workshop has at least one CMM machine to ensure machining quality and accuracy of machine parts.
However, after a period of use, errors on the parts on the CMM machine will appear. That is why it is necessary to periodically inspect or calibrate the CMM measuring machine to keep the error level within the allowable range.